Industrial Epoxy Floors That Handle Forklifts and Spills
Forklifts are tough on floors. So are chemicals, oils, and constant foot traffic. If you’re running a warehouse, production facility, or automotive shop, you’ve probably seen the damage firsthand—cracked concrete, stained surfaces, and slick areas that slow down your team and create safety risks.
Epoxy flooring is designed to handle this kind of abuse. According to OSHA, thousands of workplace slip-and-fall injuries happen each year due to unsafe flooring. A properly installed industrial epoxy system can reduce those risks while making your floors stronger, cleaner, and easier to maintain.
This article is for operations managers, business owners, and facility leads who are tired of patching problems. We’ll walk through why epoxy works in high-impact environments and how to choose the right system for your space.
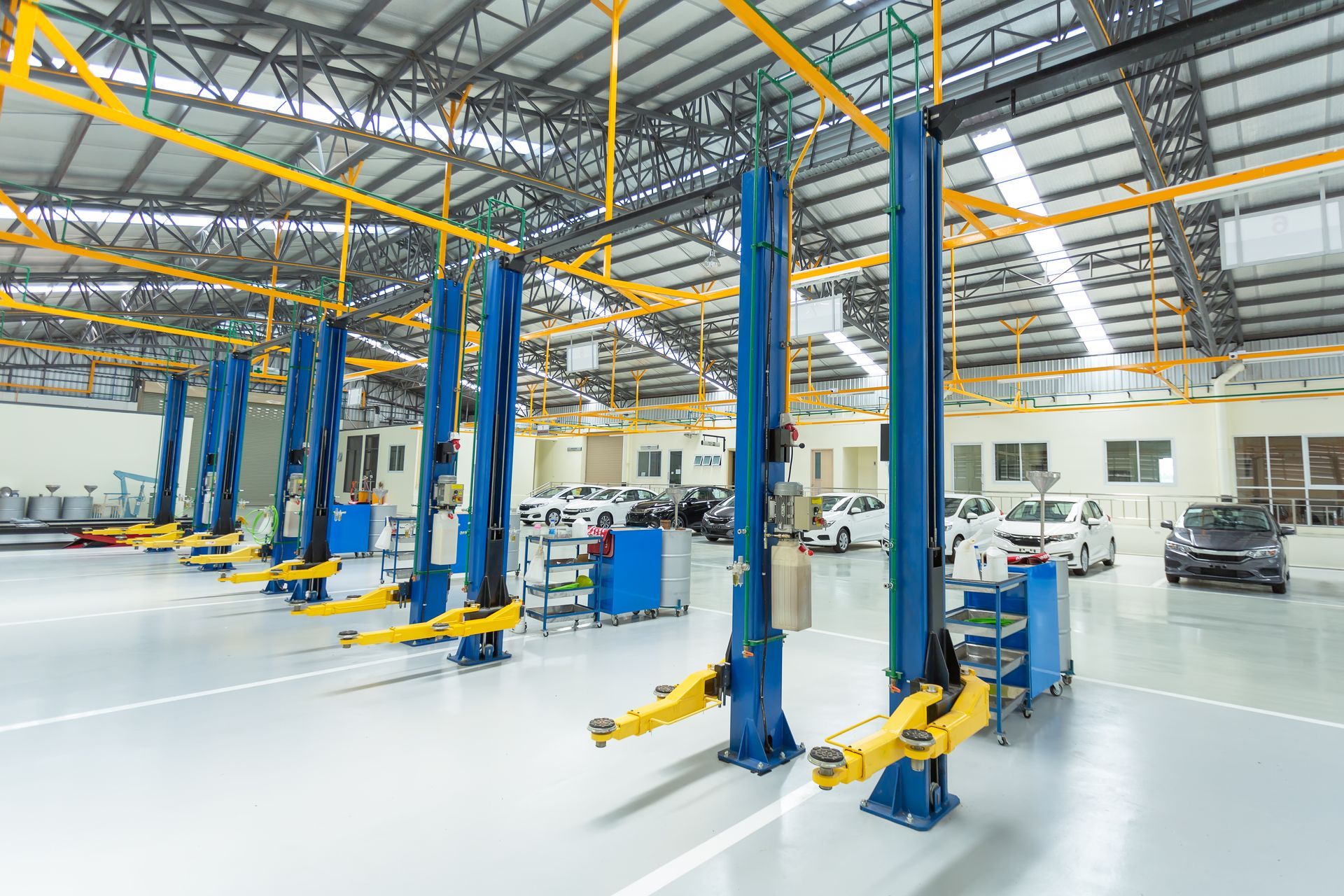
Why Concrete Alone Doesn’t Cut It in Industrial Settings
Concrete might seem tough, but in busy industrial spaces, it doesn’t hold up for long. Daily wear from machinery, chemicals, and foot traffic can quickly expose its weaknesses. Here’s what really happens behind the scenes:
- It cracks under pressure. Forklifts, loaded pallets, and constant motion cause stress fractures. Over time, these cracks grow, chip, and compromise the surface.
- It absorbs spills. Concrete is porous. Oils, fuels, coolants, and cleaning agents soak in, leaving behind stains and weakening the internal structure.
- It gets slippery. A smooth concrete floor might look clean, but it becomes hazardous when wet or greasy—raising the risk of slips and accidents.
- It’s expensive to fix. What starts as a hairline crack can turn into a costly repair if it spreads or reaches the sub-base.
If your floors already show wear, it’s not just surface damage—it’s a sign your slab is taking a beating every day.
What Makes Industrial Epoxy Different
Not all epoxy flooring is built for heavy-duty use. The kind you see in home garages or showrooms might look nice, but it won’t stand a chance in a high-traffic industrial environment. Industrial epoxy systems are engineered to perform under pressure—literally.
These coatings are thicker, tougher, and made with high solids content for maximum durability. In many cases, they’re reinforced with urethane or polyaspartic topcoats that add even more resistance to the kind of abuse seen in warehouses, manufacturing plants, and production floors.
They’re designed to take on:
- Constant forklift traffic
- Dragging pallets and loaded carts
- Hot tire pickup from machinery
- Harsh solvents, acids, and industrial cleaners
- Oil, grease, and chemical spills
- Sudden temperature changes in food or beverage processing
What do you get from all this?
- Impact resistance that stands up to dropped tools and heavy equipment
- Chemical protection that won’t wear away from battery acid or degreasers
- Fast, simple cleanup thanks to a smooth, sealed surface
- Non-slip options for safer movement even when wet
This isn’t just a coating—it’s a long-term flooring system that protects your investment and keeps operations moving without constant patchwork or repairs.
How Forklift Traffic Affects Floors
A fully loaded forklift can weigh over 9,000 pounds. Multiply that by dozens of passes a day, and you’ve got a serious stress test.
Forklifts do more than roll—they grind. The small, hard tires create point loads that push dirt and debris into concrete pores. Over time, this leads to:
- Surface abrasion
- Microcracking
- Delamination of coatings (if not installed properly)
Epoxy coatings built for forklift zones often include:
- Multiple layers: Primer, midcoat, and topcoat for added thickness
- Quartz or flake broadcast: Adds grip and durability
- Moisture vapor barriers: Prevents failures from below the surface
Investing in the right floor from the start saves you money on repairs and downtime later.
Spills Happen—Is Your Floor Ready?
From hydraulic fluid to harsh cleaners, many industrial facilities deal with chemical exposure daily. Epoxy floors act as a barrier between your concrete slab and whatever hits the surface.
Some epoxy systems are even FDA-approved for food and beverage plants, where cleaning chemicals and temperature changes are a constant.
A properly installed epoxy floor:
- Won’t absorb spills
- Won’t break down from acids, bleach, or degreasers
- Keeps the surface smooth and sealed
Add cove bases to seal off wall edges, and you’ve got a full containment system that’s easy to sanitize and inspect..
Common Applications for Heavy-Duty Epoxy Floors
Industrial epoxy floors aren’t just tough—they’re versatile. Businesses across a wide range of industries rely on them to handle constant traffic, heavy equipment, and challenging conditions without breaking down. Here are some of the most common places where industrial epoxy shines:
Common Applications for Heavy-Duty Epoxy Floors
Warehouses
Constant forklift use, pallet movement, and foot traffic call for a floor that won’t crack under pressure or become a safety hazard.
Distribution Centers
Fast-paced logistics need smooth, durable surfaces that support efficiency and resist damage from rolling carts and conveyor systems.
Airplane Hangars
These spaces require resistance to aviation fuel, oil leaks, and abrasion—plus smooth surfaces that make inspections and maintenance easier.
Manufacturing Plants
From metal shops to electronics, manufacturing floors need systems that stand up to heat, chemicals, and repeated impact.
Cold Storage Rooms
Epoxy systems in these areas must withstand thermal shock from freezing temperatures and frequent washdowns.
Automotive Shops and Dealerships
Oils, greases, tire marks, and tools demand a surface that’s easy to clean, stain-resistant, and non-slip.
Every space has different challenges. That’s why a qualified epoxy flooring contractor should assess your specific needs and recommend a system designed to handle your environment—not just install whatever’s on the shelf.
How to Know If It’s Time to Upgrade
You don’t have to wait until the floor is falling apart. If you’re seeing any of the following, it’s time to talk epoxy:
- Cracks and spalling that keep growing
- Regular slip hazards near entry points or wash stations
- Stains that never fully come clean
- Equipment vibrations that feel worse over time
- Employees complaining about uneven flooring
You might not need a full floor replacement either—many damaged concrete surfaces can be repaired and
re-coated with the right prep and product.
Installation Timeline and What to Expect
Industrial epoxy floors are usually installed over a weekend or during off-hours to avoid downtime.
Here’s what the process looks like:
- Surface prep: Diamond grinding or shot blasting to remove contaminants and open pores
- Crack repair and patching
- Primer application: Bonds the coating to the slab
- Midcoat and aggregate (optional): Adds thickness and durability
- Topcoat: Seals the system and adds chemical/UV resistance
- Cure time: Depending on the product, floors are ready in 24–72 hours
Ask about fast-cure systems if your operations can’t shut down for long. Some polyaspartic floors are ready for forklift traffic within 24 hours.
How Much Does an Industrial Epoxy Floor Cost?
Here’s a rough estimate of common industrial epoxy floor systems and their average cost per square foot, based on industry standards. Prices vary depending on surface condition, size of the space, specific additives, and cure times.
Epoxy Floor System Type | Best For | Estimated Cost (Per Sq Ft) |
---|---|---|
Basic Epoxy Coating (Single Layer) | Light-duty areas, low traffic | $3.00 – $5.00 |
High-Build Epoxy (2-3 Coats) | Warehouses, distribution centers | $4.50 – $7.00 |
Epoxy with Urethane Topcoat | Forklift zones, automotive shops | $5.50 – $8.00 |
Epoxy with Quartz or Flake Broadcast | Slip resistance, decorative finish | $6.00 – $9.00 |
Chemical-Resistant Epoxy System | Labs, food plants, chemical storage | $7.00 – $10.00 |
Thermal Shock Resistant Epoxy | Cold storage, processing facilities | $8.00 – $12.00 |
Fast-Cure Polyaspartic or Polyurethane | Minimal downtime, heavy-duty areas | $9.00 – $12.00+ |
Why the Right Contractor Matters
You can have the best product in the world, but poor prep or rushed install = failure.
A reliable epoxy contractor should:
- Conduct moisture and hardness tests
- Recommend the right system for your environment
- Handle repairs and prep properly
- Provide a warranty on materials and labor
This isn’t a job for a painting crew or weekend handyman. Forklift-ready epoxy takes experience, industrial-grade tools, and real-world knowledge.
Conclusion
If your facility needs a floor that won’t crack under forklift pressure or soak up every spill, industrial epoxy is the clear choice. It’s safer, stronger, and easier to clean—while reducing your maintenance costs in the long run.
Zachary Daniel Concrete specializes in epoxy flooring systems that hold up in the toughest commercial and industrial environments. From high-traffic warehouses to chemical-heavy work zones, we deliver solutions that work as hard as you do.
Contact us today to get a quote and get the job done right.
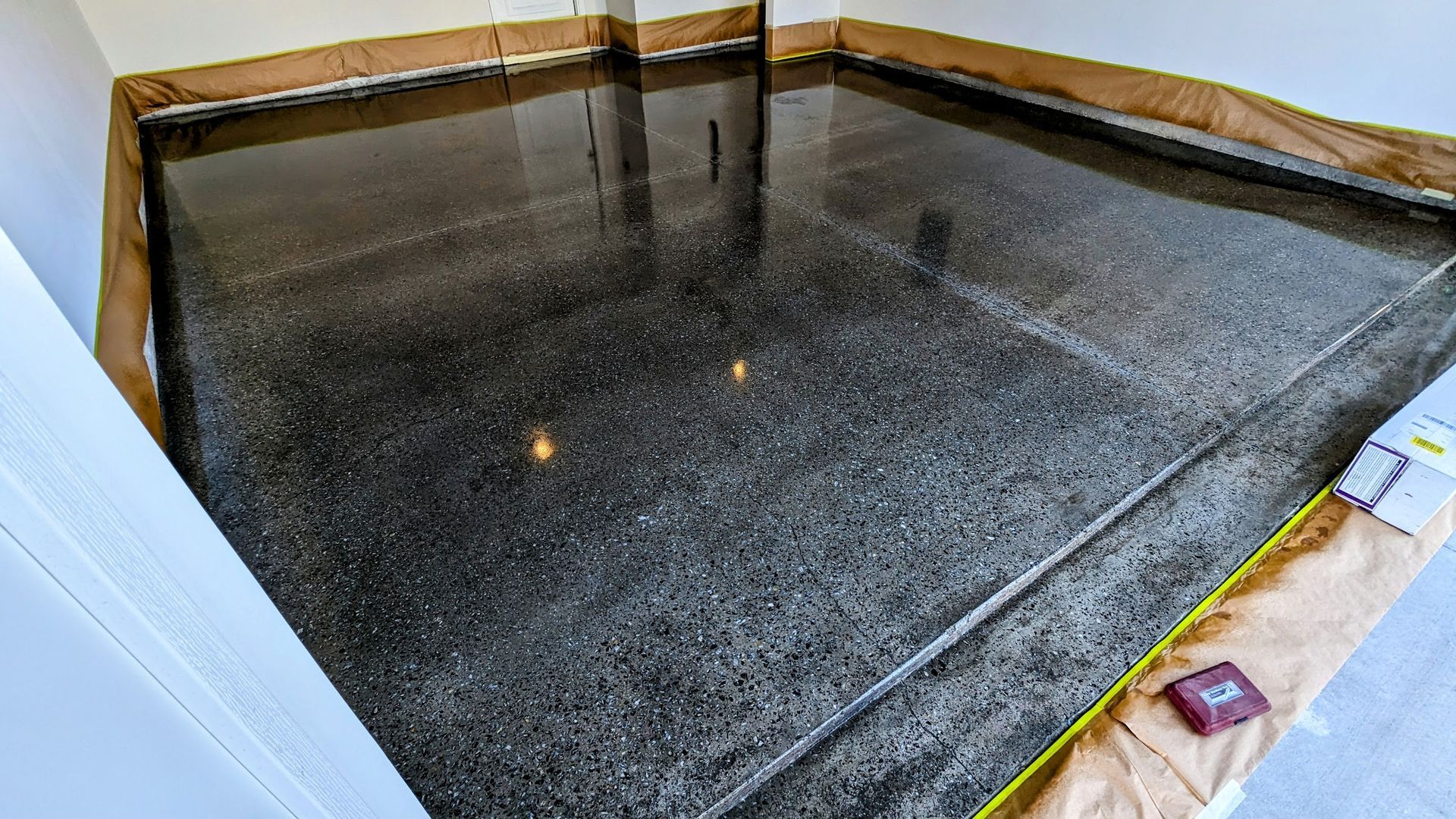
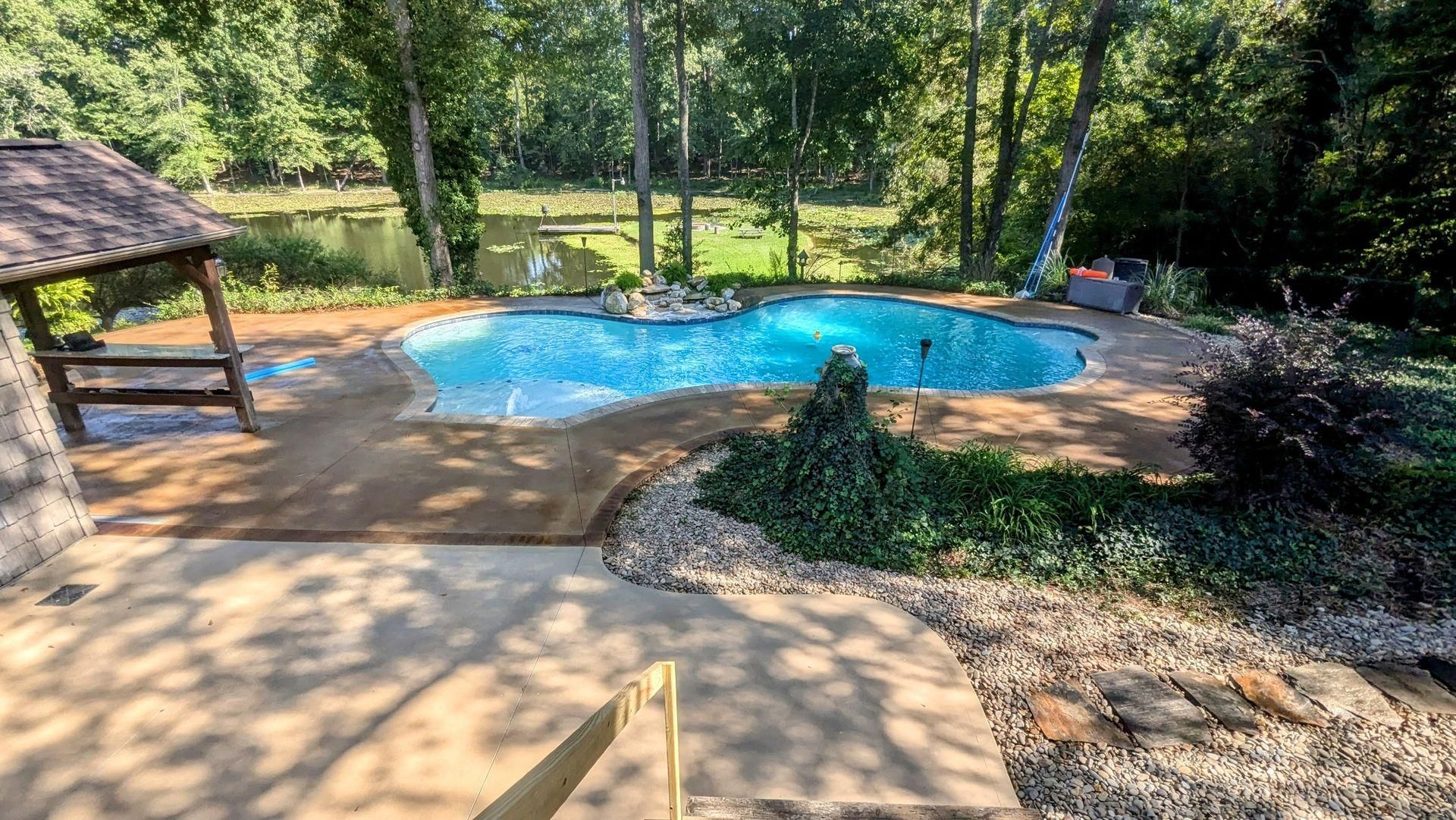
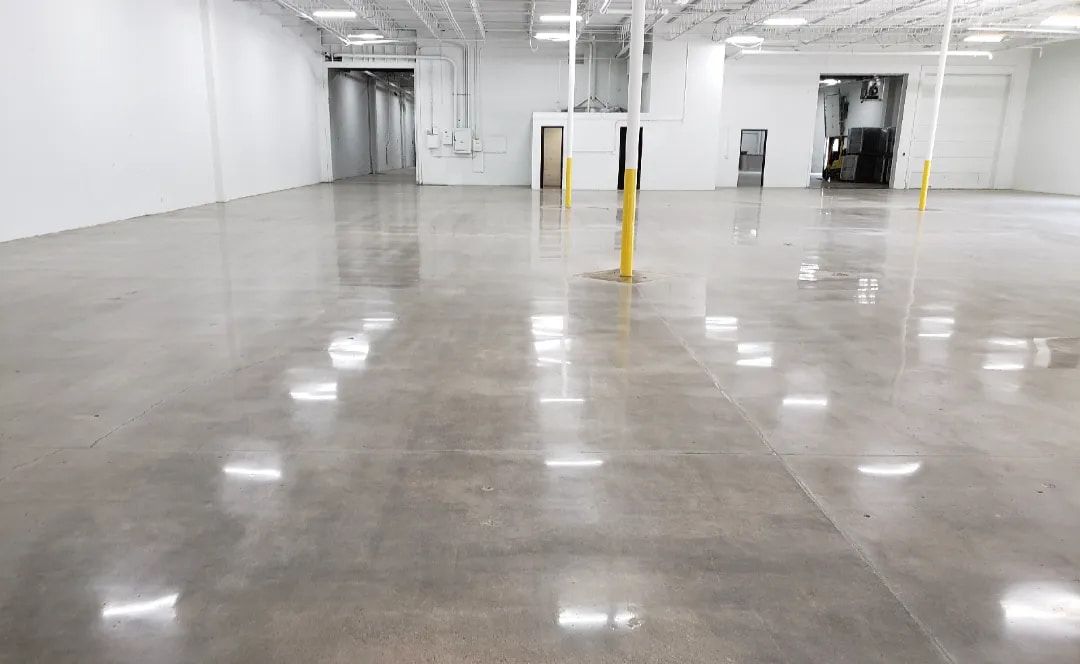